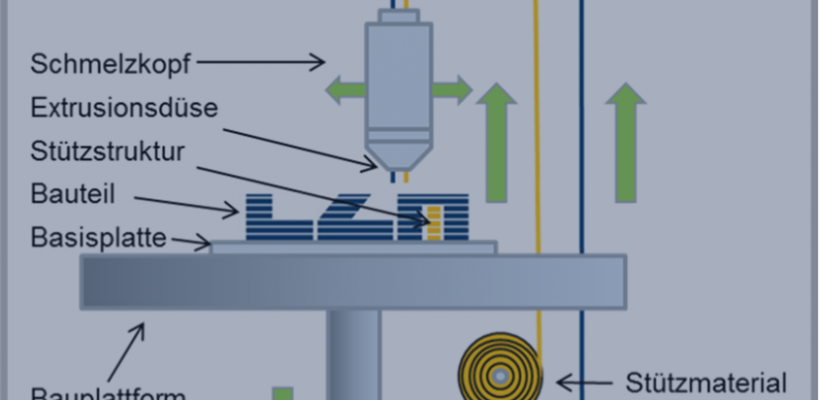
15) Welche Verfahren gibt es für den 3D-Druck von Kunststoff?
Wie schon in den Kapiteln 9) bis 12) ausgeführt, kann die Additive Fertigung wirtschaftliche Vorteile bringen. Entscheidende Faktoren sind unter anderem die Stückzahl und die Bauteilgeometrie.
Interessierte Unternehmen können die Additive Fertigung von Kunststoffen relativ kostengünstig testen und erste Erfahrungen sammeln, da einfache Desktopgeräte bereits für einige hundert Euro erhältlich sind. Im Folgenden geben wir einen Überblick über die aktuell bedeutendsten 3D-Druckverfahren für Kunststoffe.
Stereolithographie (Abkürzungen: SLA, μ-SLA, DLP)
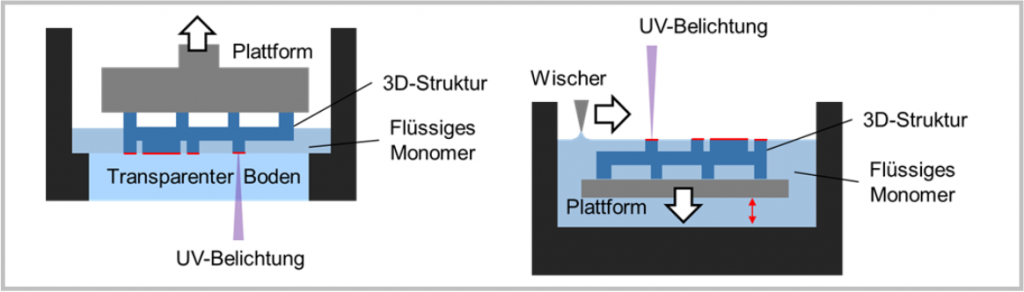
Die Stereolithographie, Mikrostereolithographie (μ–SLA), 2–Photonen–Polymerisation (2PP) und das Digital Light Processing (DLP) sind lithographische Verfahren. Mit diesen werden Bauteile aus flüssigem Kunststoff hergestellt, indem dieser mit ultraviolettem Licht oder – im Fall der 2PP – ultrakurzen Laserpulsen bestrahlt wird. Hierfür eignen sich deshalb ausschließlich flüssige Materialien, die auf Lichteinstrahlung reagieren, indem sich niedermolekulare Moleküle (Monomere) zu Makromolekülen vernetzen und so ein Polymer bilden. Durch die Vernetzung härtet das Material im bestrahlten Bereich aus.
Diese Verfahren unterscheiden sich hauptsächlich durch die Auflösung der Bauteile und die daraus resultierende Geschwindigkeit, mit der die Bauteile gefertigt werden. Grundsätzlich gilt:
Je höher die Auflösung, desto länger dauert der Druckprozess.
Beim 2PP–Verfahren lässt sich die Struktur des Bauteils direkt in das flüssige Kunststoffbad „schreiben“. Eine Besonderheit bei der 2PP ist, dass das Bauteil nicht Schicht für Schicht erstellt wird, sondern direkt dreidimensional im Polymerbad entsteht.
Bei der (μ)–Stereolithographie wird das Bauteil an eine Plattform angebunden und das Polymer an der Grenzfläche zum anliegenden Medium schichtweise polymerisiert. Das Bild zeigt links ein Verfahren, bei dem die Aushärtung durch einen transparenten Boden erfolgt.
Vorteile:
- Die Bauteilgröße wird nicht durch die Tiefe des Polymerbads limitiert,
- es wird kein zusätzlicher Wischer benötigt und
- die Schichtdicke ist durch die Distanz zwischen Bauteil und Boden klar definiert.
Nachteil:
- Beim Ablösen des Bauteils von der transparenten Platte treten Abzugkräfte auf, die zur Beschädigung filigraner Strukturen führen können.
Im Bild rechts ist das ursprüngliche Verfahren dargestellt, bei dem das Bauteil in das Polymerbad abgesenkt wird. Hierfür ist ein hinreichend tiefes Polymerbad und damit entsprechend viel flüssiges Polymer erforderlich.
Digital Light Processing
Das Digital Light Processing ist ein spezielles Stereolithographie–Verfahren. Auch hierbei entsteht das Bauteil aus flüssigem Kunststoff, der mit UV–Licht bestrahlt und ausgehärtet wird. Der Unterschied zu den übrigen stereolithografischen Verfahren ist, dass die zu belichtende Struktur nicht selektiv und punktuell bestrahlt wird, sondern direkt flächig.
Hierbei kommt als Lichtquelle z.B. ein UV–LED–Array zum Einsatz. Zahlreiche steuerbare Mikrospiegel reflektieren das Licht entweder auf das flüssige Polymer oder in einen Lichtabsorber und erzeugen so die zu belichtende Struktur. Das DLP–Verfahren ähnelt damit einem Maskenverfahren mit flexiblen Masken.
Vorteile gegenüber der konventionellen Stereolithographie:
- Die definierte flächige Belichtung bringt eine erhebliche Zeitersparnis mit sich.
- Die Herstellung im flüssigen Polymer ermöglicht durch die Polymerisation dünner Schichten eine hohe vertikale Auflösung von 0,012 mm Schichtdicke.
Die horizontale Auflösung wird durch den Projektor limitiert. Mit hochauflösenden Projektoren sind auch horizontal vergleichbare Auflösungen möglich. Dennoch bleibt die charakteristische Clusterstruktur erkennbar.
Fused Deposition Modeling (FDM) – Filamentdruck
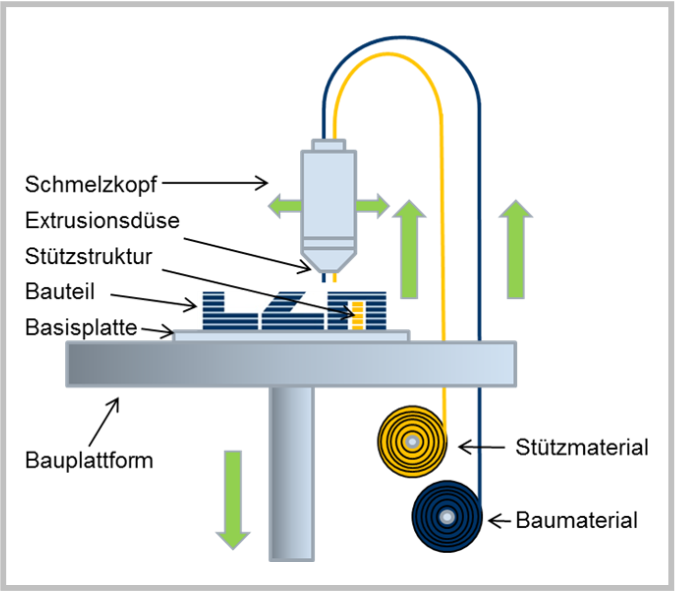
Bei diesem Verfahren ist das Ausgangsmaterial ein Kunststoffdraht (Filament), der in einer Ex-truderdüse aufgeschmolzen wird. Aus dem flüssigen Material entsteht das gewünschte Bauteil Schicht für Schicht im Direktdruck.
Vorteile dieses Verfahrens:
- Hohe Reproduzierbarkeit
- Gute Prozessstabilität
- Verwendbarkeit von technischen Kunststoffen wie ABS, PC und dem Hochleistungskunststoff ULTEM
In beheizbaren Düsen werden amorphe Thermoplaste aufgeschmolzen und die Polymerschmelze direkt in der Bauteilgeometrie schichtweise abgelegt.
Nachteil:
- Je nach Bauteilgeometrie benötigt man während des Druckprozesses Stützstrukturen zur Stabilisierung, etwa um überhängende Strukturen zu erzeugen. Diese Stützstrukturen müssen in einem späteren Arbeitsschritt entfernt werden.
Im Bild ist das FDM–Verfahren schematisch dargestellt:
Die Polymere, die als Bau–und Stützmaterial verwendet werden, werden von einer Rolle zugeführt, im Schmelzkopf aufgeschmolzen und über die Extrusionsdüse dem Prozess zugeführt.
Nach jeder Schicht wird die Bauplattform abgesenkt. Die Struktur des Bauteils entsteht in der Ebene durch die Steuerung der Düse.
Polyjet / Multijet
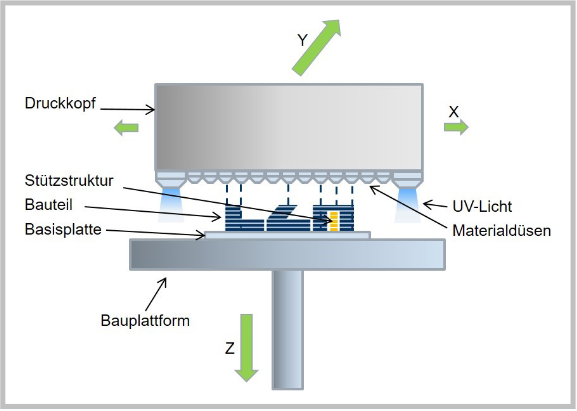
Das Polyjet–oder Multijet–Verfahren ähnelt technisch dem der Tintenstrahldrucker für den konventionellen 2D–Papierdruck. Wie beim Tintenstrahldrucker kommt ein Druckkopf zum Einsatz, der mit einer begrenzten Anzahl ansteuerbarer Düsen feinste Flüssigkeits-tropfen dosiert und punktgenau auf einer Oberfläche aufträgt.
Bei den Flüssigkeiten handelt es sich um Photopoly–mere, die mittels UV–Licht ausgehärtet (vernetzt) werden.
Vorteile:
- Wie beim Tintenstrahldruck können verschieden-farbige Photopolymere verwendet und im Druck gemischt werden.
- Auch lassen sich Photopolymere mit unterschiedli-chen Eigenschaften, wie z.B. Härte, oder in einem Waschprozess auflösbares Stützmaterial, verdrucken.
Die 3D–Bauteile entstehen durch schichtweise wiederholtes Bedrucken der gleichen Stelle in der jeweils nächsthöheren Schichtebene. Die Auflösung liegt bei den meisten Druckverfahren bei 600 dpi in der Fläche und bis zu 1814 dpi in der Schichtdicke.
Pulverbettverfahren: Selektives Laser Sintern (SLS) und Binder Jetting
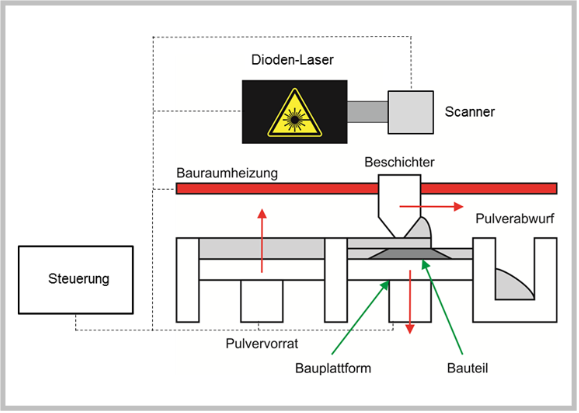
Dieses Verfahren ähnelt der Stereolithographie. Das Bauteil entsteht hierbei jedoch nicht durch den schichtweisen Aufbau an der Oberfläche eines Polymerbads, sondern an der Oberfläche eines Pulverbetts.
Vorteil:
- In beiden Fällen sind wenige oder keine Stütz-strukturen erforderlich, da das umgebende Material eine ent-sprechende Stützwirkung bietet.
Selektives Laser Sintern (SLS)
Beim Polymerbadverfahren löst UV–Strahlung die Vernetzung des flüssigen Polymers aus. Beim Pulverbettverfahren hingegen wird pulverförmiges Material thermisch versintert. Aufgeschmolzen wird das Pulver durch einen Laserstrahl.
Binder Jetting
Hierbei wird das Pulver schichtweise durch ein Binde–mittel verbunden und nicht aufgeschmolzen. Anstelle des Laserstrahls wird die Pulverschicht mit dem Binder, ähnlich wie bei einem Tintenstrahldrucker, bedruckt.
Vorteil:
- Mit farbigen Bindern lässt sich sogar mehrfarbig in 3D drucken.
Möglichkeiten zur Nachbearbeitung
Die verklebten und versinterten Druckteile weisen häufig noch unerwünschte Hohlräume auf. Abhilfe schaffen diese Nachbearbeitungsverfahren:
Verschmelzen in einem Ofenprozess
Nachteil: Die Verfestigung verursacht einen Materialschrumpf. Dieser muss bereits bei der Auslegung des Bauteils konstruktiv berücksichtigt werden.
Infiltrieren der Hohlräume
Mit Wachs, Epoxid–Harzen, Acryl, Polyurethanen oder anderen Materialien lassen sich die finalen Bauteile infiltrieren und so die Materialeigenschaften anpassen und die Oberflächen verbessern.